近期,国家发展改革委、工业和信息化部、生态环境部、国家能源局四部门发布了《高耗能行业重点领域节能降碳改造升级实施指南(2022年版)》的通知,其中包括《水泥行业节能降碳改造升级实施制指南》,指出水泥行业是国民经济发展的重要基础原材料产业,在促进国家经济建设和国防安全中起到了重要作用,提出要“加强先进技术攻关,积极开展水泥行业节能低碳技术发展路线研究,加快研发绿色氢能煅烧水泥熟料关键技术,加快先进适用节能低碳技术产业化应用”;与此同时,为进一步推动建材行业绿色低碳高质量发展,中国建材联合会开展了“揭榜挂帅”科技项目攻关工作,其中,中国科学院大连化学物理研究所(以下简称“大连化物所”)和中材节能共同申报和承担的“双供氢系统水泥熟料氢能煅烧及窑炉烟气CO2转化利用研究”具有重大的创新性和广泛的应用性,受到了行业内外的普遍关注。
我国现有水泥熟料生产线约2千条,2021年水泥熟料生产达到15多亿吨,由煤炭消耗产生的CO2排放接近3.5亿吨,采用非化石能源代替燃煤煅烧水泥熟料、减少直接CO2排放是水泥行业及水泥生产企业面临的紧迫任务。事实上,随着我国清洁能源的发展,非化石能源产出和应用已得到了快速增长,预计在2030年风力、太阳能发电量可达11万亿kWh。然而,水泥熟料煅烧需要燃料燃烧产生热量,再通过传导、辐射和对流进行热交换,以满足水泥熟料矿物形成的热动力学反应条件,这就需要将非化石能源转化成绿色燃料,送入水泥窑炉中进行燃烧放热,而绿氢则是这种能源转化的最佳选择。目前,国际上的一些水泥集团公司也正偿试采用绿氢代替燃煤进行水泥熟料煅烧。例如,墨西哥西麦斯水泥在西班牙的水泥厂大多采用电解水制氢、氢能替代燃煤用量达20%;德国海德堡水泥在英国的一家水泥厂采用液氢代替燃煤、替代率接近40%。
由大连化物所等单位提出的绿氢煅烧水泥熟料技术路线,其最终目标则是要实现水泥熟料煅烧所用燃煤的全部替代,并实现窑炉烟气CO2捕集利用。这首先是通过风力、光伏发电和水电的输入,采用高效电解水技术制备氢气和氧气,随后将氢气和氧气由特制的多射流燃烧器喷入到水泥窑炉中混合燃烧、即煅烧水泥熟料,排出窑炉的烟气进行水汽和二氧化碳分离,分离的水汽冷凝后返回到电解水槽中进行循环使用,分离的二氧化碳则可采用加氢制备甲醇、或是制备其他工业产品;窑炉工艺流程布置如图一所示。
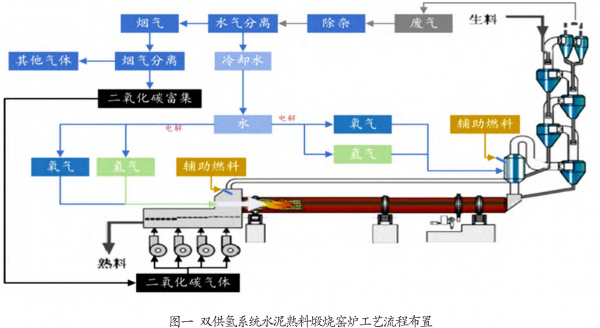
图一 双供氢系统水泥熟料煅烧窑炉工艺流程布置
“双供氢系统水泥熟料氢能煅烧及窑炉烟气CO2转化利用”这一技术路线,既适应了我国清洁能源发展,又使得既有水泥生产技术装备基本保持不变,为水泥生产企业带来的节能降碳作用也非常显著,相关研究工作主要包括高效电解水制氢技术、绿氢煅烧水泥熟料窑炉工艺技术和窑炉烟气CO2分离及加氢制备甲醇技术等三个部分。
如图二所示,电解水制氢技术的原理比较简单,即是将水在直流电的作用下分解,进而在阴阳极板上分别产生氢气和氧气,随后再进行气液分离。根据电解槽隔膜材料的不同,电解水制氢分为碱性槽法、质子交换膜(PEM)法和高温固体氧化法等,而应用广泛、且效率较高的是PEM法。针对绿氢煅烧水泥熟料这一工业性应用,大连化物所项目研究团队将对质子交换膜材料,析氢、氧催化剂材料和膜电极材料进行更深入的研发,以实现大产出、高效率电解水制氢技术工程化应用。
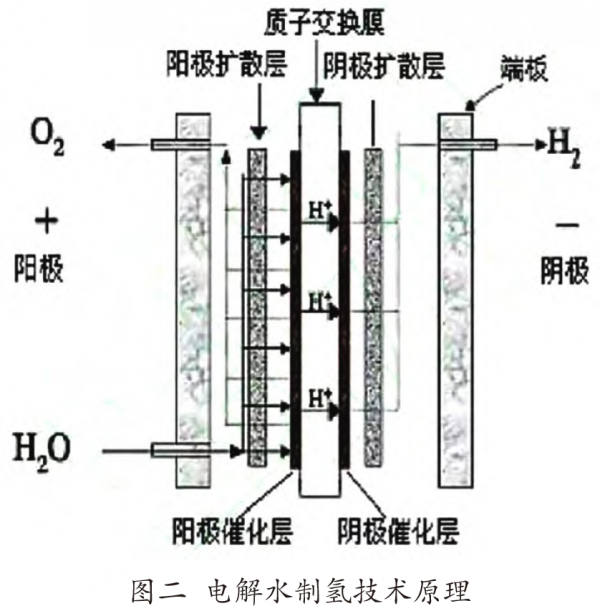
图二 电解水制氢技术原理
绿氢煅烧水泥熟料窑炉工艺技术包括新型氢、氧混合燃烧器的开发,窑炉内热传递过程调控,烟气CO2分离及循环工艺等。绿氢燃烧与燃煤燃烧在单位热值、燃烧速率、热流密度等方面都有较大的不同,这就需要模拟分析和研究设计全新的氢、氧混合燃烧器,满足水泥熟料煅烧所需的热力强度,同时通过在线监测和智能反馈,实现水泥窑炉内热能的优化配置,获得节能降碳的多重效果。此外,基于氢、氧燃烧前后气体量的变化及窑炉内气-固两相流的模拟分析,研究团队还将研发全新的烟气CO2分离技术,分析CO2循环量及其烟气CO2分压的变化规律,确定高固气比条件下物料反应的热动力学过程,保证水泥窑炉长期高效稳定运行。
CO2加氢制备甲醇技术相对比较成熟,其优点是可以实现储能和碳氢源的循环利用,而对应的核心技术则是制备甲醇的催化剂材料,目前使用的催化剂材料尚存在CO2转化率低、成品选择性催化弱等缺点。近期,大连化物所的相关研究在这一领域取得重大突破: 针对石化行业CO2排放,研究工作经历实验室小试、百克级单管评价试验、催化剂电极放大制备、中试工艺包设计等过程,建设完成了千吨级中试装置(见图三),CO2转化率达到85%以上,合成产品选择性大于76%。尽管水泥行业CO2捕集利用与石化行业的有较大差异,但CO2催化转化机理是相同的,研究团队将在现有工作基础上,针对水泥窑炉烟气CO2特性及工艺过程,研发出相适应的高转化率、高选择性催化剂材料技术。
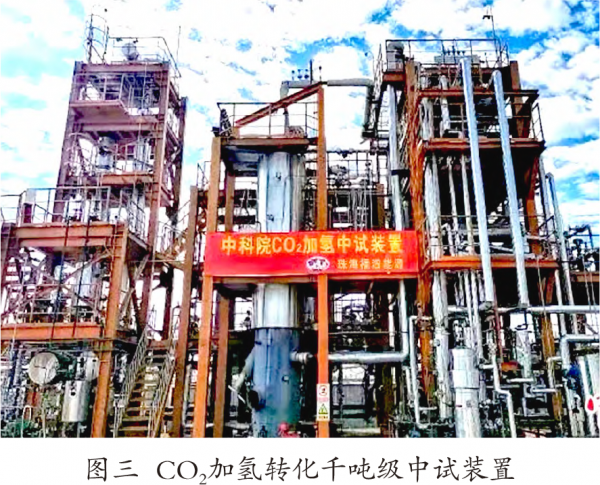
图三 CO2加氢转化千吨级中试装置
“双供氢系统水泥熟料氢能煅烧及窑炉烟气CO2转化利用研究”项目正在加速研究过程中,实验室研究初步验证了工艺技术路线的可行性,全流程中试装置已开工建设,预计今年上半年可投入运行试验,并在近年内实现研发技术集成和实际工程化应用。项目研发团队也希望先进水泥生产企业的参与和合作,“共同培育标杆示范企业”,为水泥行业节能降碳和“双碳目标”的实现提供强有力的技术支撑,为水泥行业绿色低碳高质量发展作出较大的贡献! |