张智峰,温小萍
(河南理工大学机械与动力工程学院,河南焦作454003)
摘要:该文主要针对氢气爆燃条件下安全性进行仿真研究,通过数值仿真获得不同工况下发生氢气爆燃时安全壳内压力场、温度场的空间分布与时间演化特征,获得氢气发生爆燃时作用于安全壳内壁及安全壳内完整、可信的压力、温度载荷数据,从而为安全壳及设备的力学响应分析提供输入参数。模拟结果表明,在安全壳内氢气爆燃爆轰所产生高温和高压的影响下,安全壳结构的最大变形为95.274m,最大应力约为2.6E+11Pa,远大于安全壳所用结构钢材料的屈服极限,安全壳发生塑性变形,结构遭到根本性的破坏。
在LOCA(Loss of Coolant Accident)事故工况下,锆合金包壳与水或水蒸气发生锆水反应而产生大量氢气,导致在产生源附近或者与安全壳内空气混合后可能发生燃烧、爆燃或爆炸[1-2]。在氢气产生源附近区域,如果有点火源和足够的氧气,氢气将会燃烧并且产生稳定的火焰,称为扩散燃烧。这种燃烧所产生的热量和压力峰值较小,通常不会对安全壳完整性构成威胁。在释放源附近没有发生燃烧的氢气,将与安全壳内的水蒸气、空气混合,并且在安全壳隔间传输,导致安全壳内整体或某些局部的氢气浓度升高。当安全壳内的氢气浓度达到一定比例后,在适合的外界条件下(例如温度、压力、氧气浓度等),这些混合气体将发生爆燃,并可能由此转变成爆炸,在极短时间内形成很高的压力峰值。如果未能及时采取有效的氢气缓解措施,氢气在安全壳内可能发生局部或整体性的爆燃或爆炸,由此产生的静态和动态压力载荷会危及安全壳完整性,并影响安全壳内安全系统安全功能的有效执行[3]。
数值模拟仿真是一项较为成熟的技术,针对该项目这种核反应堆安全壳爆燃等危害性极大,实验成本极高的事故,具有极强的针对性。但是安全壳内部复杂的几何结构,要实现物理模型的完全真实构建是极为不现实的,原因在于现有公开资料中仅仅给出了安全壳的整体尺寸,局部复杂微小构件的几何尺寸和安装位置均是未知的。因此,需要根据流体动力学的基础理论和实践,结合数值模拟仿真的需要,对几何模型做适当合理的简化,可以在确保计算精度的前提下,一方面简化几何模型构建难度;另一方面最大程度地降低仿真计算的工作量。
本文通过数值仿真获得不同工况下发生氢气爆燃时安全壳内压力场、温度场的空间分布与时间演化特征,获得氢气发生爆燃时作用于安全壳内壁及安全壳内完整、可信的压力、温度载荷数据,从而为安全壳及设备的力学响应分析提供输入参数。考虑到安全壳壳体结构在氢气爆燃压力作用下,产生的真实变形较小,壳体结构的变形不足以对安全壳内流场造成明显的干扰和影响,并且本报告主要目的是分析氢气爆燃对安全壳结构性能的影响,因此,在安全壳流固耦合分析过程中,可以假定为流固单向耦合过程,主要分析内流场压力对安全壳位移和应力的影响,忽略安全壳变形对内流场结构的影响特性。
1研究方法与计算模型
当固体结构变形比较大,导致流体的边界形貌发生改变后,流体分布会发生明显的变化,此时单向耦合不再合适,需要考虑固体变形对流体流动的影响。两者相互作用,最终达到一个平衡状态。ANSYS WORK-BENCH平台中双向流固耦合分析时[4],fluent计算流体工况,将耦合面上的压力数据导入到structural中,从而计算结构的应力、应变等参数,但认为变形量足够大,足以影响原先的流场形态,故将变形位移回传给fluent,从而再次计算在新的固体形状下的流场数据,得到耦合面上新的压力数据;不断重复该过程,直至计算完成。ANSYS WORKBENCH平台中双向流固耦合分析的数据流方式如图1所示。
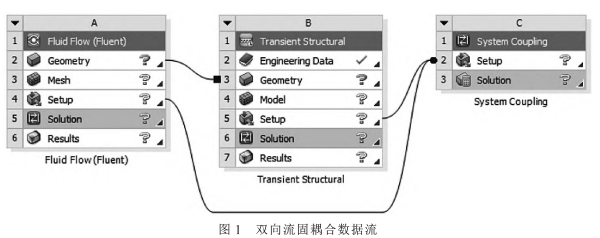
文章主要运用湍流流动模型、燃烧模型及化学反应模型。其中的湍流燃烧模型,化学反应速率是以反应进度速率的形式呈现的,反应进度量描述燃烧反应进行的程度,并不直接描述所有的化学反应[5]。反应进度量可以描述反应物的反应完全程度,是无量纲化的反应物组分浓度。对于预混火焰而言,火焰传播速度是从唯象角度描述火焰运动的一个基本参数。反应物浓度的变化率可以用表征组分浓度等值面的相对移动速度以及组分的扩散项来表示。
使用的湍流燃烧模型中,湍流燃烧传播速度的赋值是使用湍流褶皱修正因子乘层流火焰传播速度。这个赋值方法的理论基础是,湍流火焰传播速度的增大主要是因为火焰面在湍流流动作用下呈现褶皱的状态,火焰面的褶皱增大了反应面的面积,从而增大了湍流火焰的传播速度,但湍流火焰传播速度的基础仍然是火焰固有的层流火焰传播速度。湍流尺度量的获得,从流动控制方程的求解中可以得到。而火焰的基础性参数如层流火焰传播速度,火焰厚度等,则需要化学反应动力学模型求解才能得到。层流火焰传播速度,火焰厚度可以使用化学反应机理,输运参数建立一维平面火焰模型计算得到。该文章中使用Chemkin软件中的Premix模块来求解这些基础性火焰参数[6]。
仿真模拟计算的求解参数包括初始温度、热边界条件、流体域工况条件。图2为安全壳模型及网格示意图。安全壳结构的初始温度与内流场初始温度一致,为498K。安全壳的外部为空气,空气温度为297.15K。安全壳的6个外壁面为自然对流边界,对流换热系数为10W/㎡K。安全壳内氢气爆燃爆轰的CFD模拟工况为88mm稳压波动管工况,氢气浓度为0.32、氧气浓度为0.11、水蒸气浓度为0.19、初始温度493K、初始压力为1.33MPa。
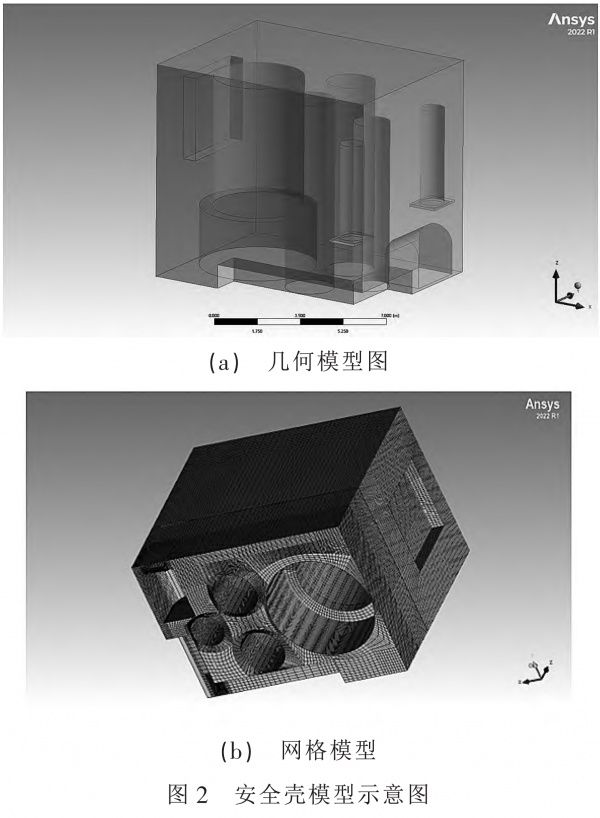
2模拟结果与讨论
2.1流场模拟结果与讨论
氢气-空气火焰的层流燃烧速率是湍流爆燃模型的一个重要输入参数。在氢气爆燃模拟计算中,使用的氢气-空气火焰的基础参数包括层流燃烧速率(Laminar burning velocity,LBV),火焰厚度,火焰绝热过程对应的变化反应级数[7]。这些基础性参数的计算使用反应动力学软件Chemkin完成。氢气-空气火焰的反应机理使用国内外广泛使用的FFCM机理。由于罐体中爆燃火焰传播对于未燃区域的压缩属于绝热压缩过程,可以将氢气-空气火焰的层流燃烧速率和温度、压力的函数关联,表示为未燃区域压力比的函数。
为了得到压缩的未燃区域氢气-空气火焰对应的层流燃烧速率,我们根据氢气-空气混合气体的绝热指数,设置一系列初始压力和温度,进而计算对应的层流燃烧速率。将这一系列的压缩的未燃区域氢气-空气层流燃烧速率拟合为5阶的多项式函数,即可在氢气-空气湍流爆燃模型中作为层流燃烧速率的输入参数使用。该工况下压缩的未燃区域氢气-空气根据FFCM反应机理计算的层流燃烧速率结果以及拟合的5阶多项式,而压缩的未燃区域氢气-空气层流燃烧速率的计算拟合多项式并作为后续湍流爆燃模型的输入参数。如图3所示为氢气-空气火焰的层流燃烧速率图,展示了不同压力比下的氢气空气火焰层流燃烧速率。该工况初始压力为1.33MPa,此时的空气氢气火焰层流燃烧速率为2.11m/s,且随压力比增加,空气氢气火焰层流燃烧速率减小。
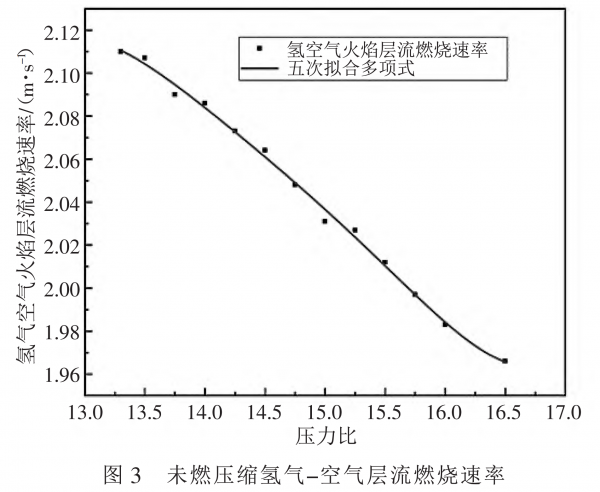
由于该工况下初始火焰层流传播速度为2.11m/s,所以该工况爆燃发生后内部流场传播十分迅速。如图4所示,在点火后0.12s时,火焰锋面在传播过程中先到达安全壳四周壁面处,在0.18s时,火焰锋面到达安全壳顶部,在0.3s时刻,整个安全壳内部温度达到最大值,随后由于壁面散热,温度逐渐开始下降,但是由于该工况爆燃十分剧烈,其温度下降并不明显。
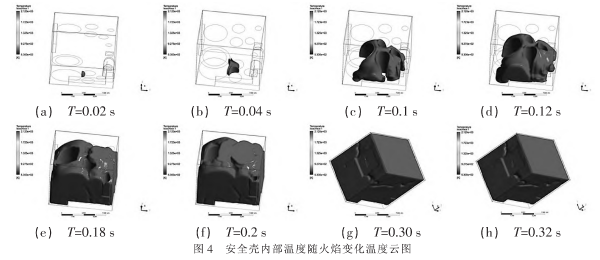
图5分为3个阶段:第一阶段为0~0.1s,此时压力变化很小,第二阶段为0.1~0.25,该时间段压力显著增大,第三阶段为0.25s之后,压力开始缓慢下降,此时内部已经达到平衡状态。结合不同时刻安全壳内部温度云图可知,氢气爆燃对应的超压变化大致分为3个阶段。第一阶段,火焰传播占据的已燃区域尺度远小于安全壳的尺度,爆燃火焰的膨胀作用导致的封闭空间压力升高很小,相应的此时安全壳内超压值相比超压峰值几乎可以忽略,如爆燃火焰的尺度为安全壳尺度的10%,已燃区域体积占安全壳体积约为0.1%,此时超压值约为初始压力的0.3%,为超压峰值的0.1%,在超压曲线中几乎分辨不出。第二阶段,爆燃火焰占据的已燃区域尺度和安全壳尺度为同一个量级,此时已燃区域的气体膨胀效应会显著影响封闭空间的压力,相应的安全壳内的超压值开始显著增大,超压增长率最大时刻即在第二阶段。第三阶段,爆燃火焰接触安全壳顶部壁面,超压值达到峰值,为0.75MPa,安全壳外壁的散热导致安全壳内气体温度逐渐降低,超压值开始降低。

2.2安全壳完整性结果与讨论
基于安全壳结构热力学特性仿真结果,给出0.03、0.18和0.39s时刻的安全壳温度及热通量分布如图6所示。从图中可以看出,安全壳结构的最低温度随氢气爆燃的时间增加而增大,从0.03s的198.73℃开始最终增大到0.39s的1512.8℃。0.3s之前,最低温度的增长速率较小,而0.3s之后则急剧增加。随着时间的增加,安全壳的最高温度存在局部波动,但是整体上呈现出先增大后减小的变化趋势,峰值温度出现在0.18s的时刻,峰值为3959.9K。随着时间的增加,热流密度呈现出先增大后减小的变化趋势,热流密度先是从0.03s的812100W/㎡迅速增大到0.18s的峰值12565000W/㎡,而后逐渐减小,最终减小为0.39s的1414100W/㎡。热流密度的最小值则整体上随时间的增大而增大,但在0.30s和0.33s出现局部的减小情况。
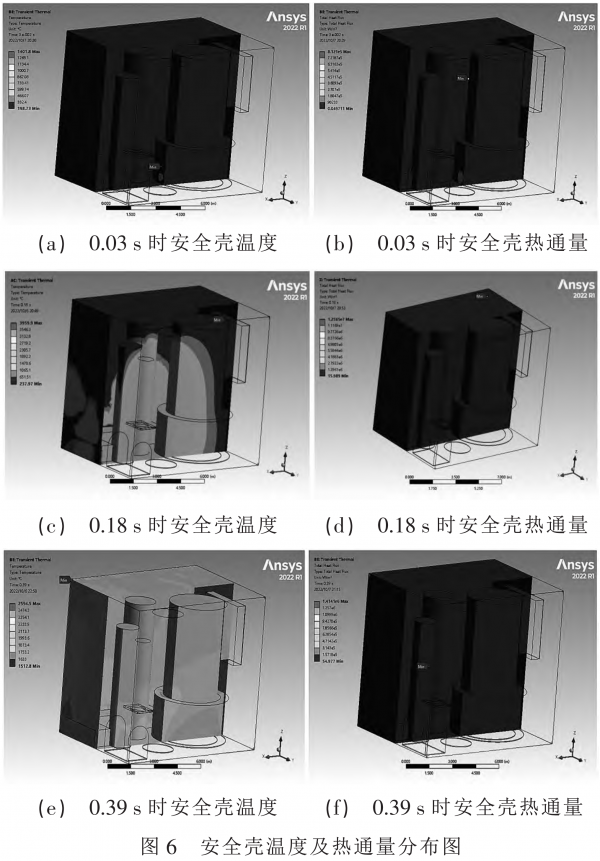
基于安全壳结构动力学特性仿真结果,给出0.03、0.18和0.39s时刻的安全壳变形位移及结构应力分布如图7所示。从图中可以看出,由于底面施加了固定约束,底面的位移为0m。安全壳结构的最大变形随时间的增加而增大,0.39s时刻最大变形量为95.274m,可知安全壳结构已经发生了塑性变形,安全壳结构已经遭到结构性破坏。随着时间的增加,安全壳的结构应力的极大值整体呈现增大变化趋势,最大应力出现在0.39s时刻,约为2.6E+11Pa。考虑到结构钢的屈服强度为235MPa,可知安全壳的最大应力远大于材料的屈服极限,安全壳发生了塑性变形,结构遭到破坏。
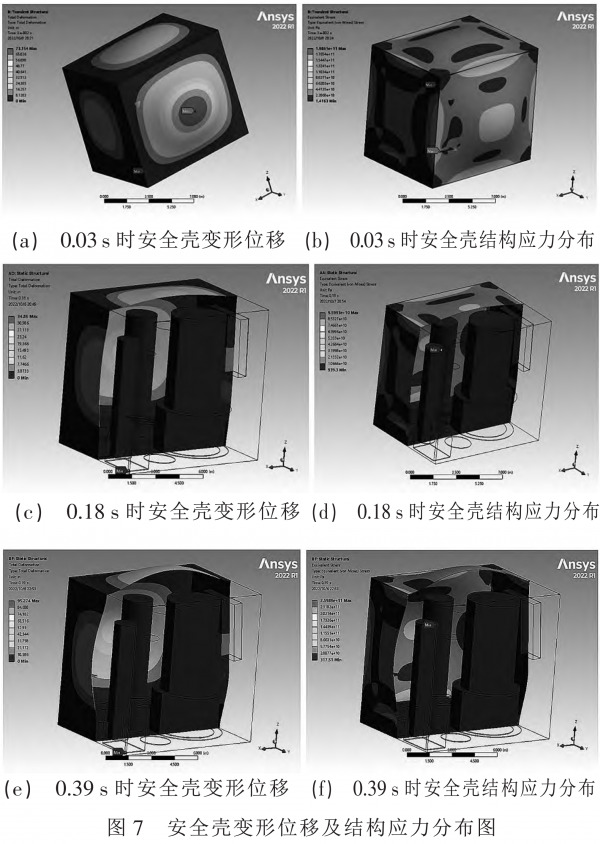
3结论
文章主要针对氢气爆燃条件下安全性进行仿真研究,通过对安全壳内部氢气爆燃事故工况下爆燃条件进行数值模拟仿真计算,得到如下结论。
1)安全壳内氢气等混合气体被点燃后,呈现出球形火焰锋面,并向外传播,但由于安全壳的内部有许多不规则形状障碍物,火焰锋面在传播过程中的形状逐渐偏离球形,其流动也由紊流变为湍流。火焰在传播过程中会先传至四周壁面,然后再顶部壁面,随后充满整个安全壳内部,此时温度达到最大,之后由于壁面散热,整个安全壳内部温度趋近于平衡。
2)结合不同时刻安全壳内部温度云图可知,氢气爆燃对应的超压变化大致分为3个阶段。第一阶段,火焰传播占据的已燃区域尺度远小于安全壳的尺度,爆燃火焰的膨胀作用导致的封闭空间压力升高很小,相应的此时安全壳内超压值相比超压峰值几乎可以忽略,例如爆燃火焰的尺度为安全壳尺度的10%,已燃区域体积占安全壳体积约为0.1%,此时超压值约为初始压力的0.3%,为超压峰值的0.1%,在超压曲线中几乎分辨不出。第二阶段,爆燃火焰占据的已燃区域尺度和安全壳尺度为同一个量级,此时已燃区域的气体膨胀效应会显著影响封闭空间的压力,相应的安全壳内的超压值开始显著增大,超压增长率最大时刻即在第二阶段。第三阶段,爆燃火焰接触安全壳壁面,超压值达到峰值,安全壳外壁的散热导致安全壳内气体温度逐渐降低,超压值开始降低。
3)在安全壳内氢气爆燃爆轰所产生高温和高压的影响下,安全壳结构的最大变形为95.274m,最大应力约为2.6E+11Pa,远大于安全壳所用结构钢材料的屈服极限,安全壳发生了塑性变形,结构遭到根本性的破坏。
参考文献:
[1]袁璐,曹学武.核电厂严重事故下氢气源项的不确定性分析[J].原子能科学技术,2021,55(11):2036-2042.
[2]邓坚.大型干式安全壳严重事故条件下氢气控制研究[D].上海:上海交通大学,2008.
[3]孙洪平,张弛.AP1000核电厂严重事故下氢气安全分析[C]//中国核学会核能动力分会反应堆热工流体专业委员会,中核核反应堆热工水力技术重点实验室.第十五届全国反应堆热工流体学术会议暨中核核反应堆热工水力技术重点实验室学术年会论文集.西安交通大学核科学与核技术学院;环境保护部核与辐射安全中心,2017:10.
[4]韩刚,郭美荣,刘瑞.基于ANSYSWorkbench的双向流固耦合振动仿真方法[J].齐齐哈尔大学学报(自然科学版),2023,39(6):11-14.
[5]孙楠.CH4在O2/CO2气氛下预混火焰特性的数值模拟[D].沈阳:东北大学,2015.
[6]朱睿.掺混氢气对甲烷/空气一维层流火焰的影响[J].节能,2022,41(8):62-65.
[7]刘海清,张林瑶,邢畅,等.氢燃料特性及氢微混火焰模式分析[J/OL].中国电机工程学报,1-11[2024-06-20].https://doi.org/10.13334/j.0258-8013.pcsee.232125. |